ಲೇಸರ್ ವೆಲ್ಡಿಂಗ್
ಇತ್ತೀಚಿನ ವರ್ಷಗಳಲ್ಲಿ, ಹೊಸ ಶಕ್ತಿ ಉದ್ಯಮದ ಕ್ಷಿಪ್ರ ಅಭಿವೃದ್ಧಿಗೆ ಧನ್ಯವಾದಗಳು, ಲೇಸರ್ ವೆಲ್ಡಿಂಗ್ ಅದರ ವೇಗದ ಮತ್ತು ಸ್ಥಿರವಾದ ಅನುಕೂಲಗಳಿಂದಾಗಿ ಸಂಪೂರ್ಣ ಹೊಸ ಶಕ್ತಿ ಉದ್ಯಮವನ್ನು ವೇಗವಾಗಿ ಭೇದಿಸಿದೆ.ಅವುಗಳಲ್ಲಿ, ಲೇಸರ್ ವೆಲ್ಡಿಂಗ್ ಉಪಕರಣಗಳು ಸಂಪೂರ್ಣ ಹೊಸ ಶಕ್ತಿ ಉದ್ಯಮದಲ್ಲಿ ಹೆಚ್ಚಿನ ಪ್ರಮಾಣದ ಅನ್ವಯಿಕೆಗಳನ್ನು ಹೊಂದಿವೆ.
ಲೇಸರ್ ವೆಲ್ಡಿಂಗ್ ಅದರ ವೇಗದ ವೇಗ, ದೊಡ್ಡ ಆಳ ಮತ್ತು ಸಣ್ಣ ವಿರೂಪತೆಯ ಕಾರಣದಿಂದಾಗಿ ಜೀವನದ ಎಲ್ಲಾ ಹಂತಗಳಲ್ಲಿ ತ್ವರಿತವಾಗಿ ಮೊದಲ ಆಯ್ಕೆಯಾಗಿದೆ.ಸ್ಪಾಟ್ ವೆಲ್ಡ್ಗಳಿಂದ ಬಟ್ ವೆಲ್ಡ್ಸ್, ಬಿಲ್ಡ್-ಅಪ್ ಮತ್ತು ಸೀಲ್ ವೆಲ್ಡ್ಗಳವರೆಗೆ, ಲೇಸರ್ ವೆಲ್ಡಿಂಗ್ ಸಾಟಿಯಿಲ್ಲದ ನಿಖರತೆ ಮತ್ತು ನಿಯಂತ್ರಣವನ್ನು ಒದಗಿಸುತ್ತದೆ.ಮಿಲಿಟರಿ ಉದ್ಯಮ, ವೈದ್ಯಕೀಯ ಆರೈಕೆ, ಏರೋಸ್ಪೇಸ್, 3C ಆಟೋ ಭಾಗಗಳು, ಮೆಕ್ಯಾನಿಕಲ್ ಶೀಟ್ ಮೆಟಲ್, ಹೊಸ ಶಕ್ತಿ ಮತ್ತು ಇತರ ಕೈಗಾರಿಕೆಗಳು ಸೇರಿದಂತೆ ಕೈಗಾರಿಕಾ ಉತ್ಪಾದನೆ ಮತ್ತು ಉತ್ಪಾದನೆಯಲ್ಲಿ ಇದು ಪ್ರಮುಖ ಪಾತ್ರ ವಹಿಸುತ್ತದೆ.
ಇತರ ವೆಲ್ಡಿಂಗ್ ತಂತ್ರಜ್ಞಾನಗಳೊಂದಿಗೆ ಹೋಲಿಸಿದರೆ, ಲೇಸರ್ ವೆಲ್ಡಿಂಗ್ ಅದರ ವಿಶಿಷ್ಟ ಅನುಕೂಲಗಳು ಮತ್ತು ಅನಾನುಕೂಲಗಳನ್ನು ಹೊಂದಿದೆ.
ಅನುಕೂಲ:
1. ವೇಗದ ವೇಗ, ದೊಡ್ಡ ಆಳ ಮತ್ತು ಸಣ್ಣ ವಿರೂಪ.
2. ವೆಲ್ಡಿಂಗ್ ಅನ್ನು ಸಾಮಾನ್ಯ ತಾಪಮಾನದಲ್ಲಿ ಅಥವಾ ವಿಶೇಷ ಪರಿಸ್ಥಿತಿಗಳಲ್ಲಿ ನಿರ್ವಹಿಸಬಹುದು, ಮತ್ತು ವೆಲ್ಡಿಂಗ್ ಉಪಕರಣವು ಸರಳವಾಗಿದೆ.ಉದಾಹರಣೆಗೆ, ಲೇಸರ್ ಕಿರಣವು ವಿದ್ಯುತ್ಕಾಂತೀಯ ಕ್ಷೇತ್ರದಲ್ಲಿ ಅಲೆಯುವುದಿಲ್ಲ.ಲೇಸರ್ಗಳು ನಿರ್ವಾತ, ಗಾಳಿ ಅಥವಾ ಕೆಲವು ಅನಿಲ ಪರಿಸರದಲ್ಲಿ ಬೆಸುಗೆ ಹಾಕಬಹುದು ಮತ್ತು ಗಾಜಿನ ಮೂಲಕ ಅಥವಾ ಲೇಸರ್ ಕಿರಣಕ್ಕೆ ಪಾರದರ್ಶಕವಾಗಿರುವ ವಸ್ತುಗಳನ್ನು ವೆಲ್ಡ್ ಮಾಡಬಹುದು.
3. ಇದು ಟೈಟಾನಿಯಂ ಮತ್ತು ಸ್ಫಟಿಕ ಶಿಲೆಯಂತಹ ವಕ್ರೀಕಾರಕ ವಸ್ತುಗಳನ್ನು ಬೆಸುಗೆ ಹಾಕಬಹುದು ಮತ್ತು ಉತ್ತಮ ಫಲಿತಾಂಶಗಳೊಂದಿಗೆ ಭಿನ್ನವಾದ ವಸ್ತುಗಳನ್ನು ವೆಲ್ಡ್ ಮಾಡಬಹುದು.
4. ಲೇಸರ್ ಅನ್ನು ಕೇಂದ್ರೀಕರಿಸಿದ ನಂತರ, ವಿದ್ಯುತ್ ಸಾಂದ್ರತೆಯು ಅಧಿಕವಾಗಿರುತ್ತದೆ.ಆಕಾರ ಅನುಪಾತವು 5: 1 ಅನ್ನು ತಲುಪಬಹುದು ಮತ್ತು ಹೆಚ್ಚಿನ ಶಕ್ತಿಯ ಸಾಧನಗಳನ್ನು ವೆಲ್ಡಿಂಗ್ ಮಾಡುವಾಗ 10: 1 ವರೆಗೆ ತಲುಪಬಹುದು.
5. ಮೈಕ್ರೋ ವೆಲ್ಡಿಂಗ್ ಅನ್ನು ನಿರ್ವಹಿಸಬಹುದು.ಲೇಸರ್ ಕಿರಣವನ್ನು ಕೇಂದ್ರೀಕರಿಸಿದ ನಂತರ, ಒಂದು ಸಣ್ಣ ಸ್ಥಳವನ್ನು ಪಡೆಯಬಹುದು ಮತ್ತು ನಿಖರವಾಗಿ ಇರಿಸಬಹುದು.ಸ್ವಯಂಚಾಲಿತ ಸಾಮೂಹಿಕ ಉತ್ಪಾದನೆಯನ್ನು ಸಾಧಿಸಲು ಮೈಕ್ರೋ ಮತ್ತು ಸಣ್ಣ ವರ್ಕ್ಪೀಸ್ಗಳ ಜೋಡಣೆ ಮತ್ತು ವೆಲ್ಡಿಂಗ್ಗೆ ಇದನ್ನು ಅನ್ವಯಿಸಬಹುದು.
6. ಇದು ತಲುಪಲು ಕಷ್ಟವಾದ ಪ್ರದೇಶಗಳನ್ನು ಬೆಸುಗೆ ಹಾಕಬಹುದು ಮತ್ತು ಹೆಚ್ಚಿನ ನಮ್ಯತೆಯೊಂದಿಗೆ ಸಂಪರ್ಕವಿಲ್ಲದ ದೂರದ ವೆಲ್ಡಿಂಗ್ ಅನ್ನು ನಿರ್ವಹಿಸಬಹುದು.ವಿಶೇಷವಾಗಿ ಇತ್ತೀಚಿನ ವರ್ಷಗಳಲ್ಲಿ, YAG ಲೇಸರ್ ಸಂಸ್ಕರಣಾ ತಂತ್ರಜ್ಞಾನವು ಆಪ್ಟಿಕಲ್ ಫೈಬರ್ ಟ್ರಾನ್ಸ್ಮಿಷನ್ ತಂತ್ರಜ್ಞಾನವನ್ನು ಅಳವಡಿಸಿಕೊಂಡಿದೆ, ಇದು ಲೇಸರ್ ವೆಲ್ಡಿಂಗ್ ತಂತ್ರಜ್ಞಾನವನ್ನು ಹೆಚ್ಚು ವ್ಯಾಪಕವಾಗಿ ಪ್ರಚಾರ ಮಾಡಲು ಮತ್ತು ಅನ್ವಯಿಸಲು ಸಕ್ರಿಯಗೊಳಿಸಿದೆ.
7. ಲೇಸರ್ ಕಿರಣವು ಸಮಯ ಮತ್ತು ಜಾಗದಲ್ಲಿ ವಿಭಜಿಸಲು ಸುಲಭವಾಗಿದೆ, ಮತ್ತು ಅನೇಕ ಕಿರಣಗಳನ್ನು ಏಕಕಾಲದಲ್ಲಿ ಅನೇಕ ಸ್ಥಳಗಳಲ್ಲಿ ಸಂಸ್ಕರಿಸಬಹುದು, ಹೆಚ್ಚು ನಿಖರವಾದ ಬೆಸುಗೆಗೆ ಪರಿಸ್ಥಿತಿಗಳನ್ನು ಒದಗಿಸುತ್ತದೆ.
ದೋಷದ:
1. ವರ್ಕ್ಪೀಸ್ನ ಅಸೆಂಬ್ಲಿ ನಿಖರತೆಯು ಹೆಚ್ಚಿನದಾಗಿರಬೇಕು ಮತ್ತು ವರ್ಕ್ಪೀಸ್ನಲ್ಲಿನ ಕಿರಣದ ಸ್ಥಾನವನ್ನು ಗಮನಾರ್ಹವಾಗಿ ವಿಚಲನಗೊಳಿಸಲಾಗುವುದಿಲ್ಲ.ಏಕೆಂದರೆ ಕೇಂದ್ರೀಕರಿಸಿದ ನಂತರ ಲೇಸರ್ ಸ್ಪಾಟ್ ಗಾತ್ರವು ಚಿಕ್ಕದಾಗಿದೆ ಮತ್ತು ವೆಲ್ಡ್ ಸೀಮ್ ಕಿರಿದಾಗಿರುತ್ತದೆ, ಫಿಲ್ಲರ್ ಲೋಹದ ವಸ್ತುಗಳನ್ನು ಸೇರಿಸಲು ಕಷ್ಟವಾಗುತ್ತದೆ.ವರ್ಕ್ಪೀಸ್ನ ಜೋಡಣೆಯ ನಿಖರತೆ ಅಥವಾ ಕಿರಣದ ಸ್ಥಾನೀಕರಣದ ನಿಖರತೆಯು ಅವಶ್ಯಕತೆಗಳನ್ನು ಪೂರೈಸದಿದ್ದರೆ, ವೆಲ್ಡಿಂಗ್ ದೋಷಗಳು ಸಂಭವಿಸುವ ಸಾಧ್ಯತೆಯಿದೆ.
2. ಲೇಸರ್ಗಳು ಮತ್ತು ಸಂಬಂಧಿತ ವ್ಯವಸ್ಥೆಗಳ ಬೆಲೆ ಹೆಚ್ಚಾಗಿರುತ್ತದೆ ಮತ್ತು ಒಂದು ಬಾರಿ ಹೂಡಿಕೆ ದೊಡ್ಡದಾಗಿದೆ.
ಲಿಥಿಯಂ ಬ್ಯಾಟರಿ ತಯಾರಿಕೆಯಲ್ಲಿ ಸಾಮಾನ್ಯ ಲೇಸರ್ ವೆಲ್ಡಿಂಗ್ ದೋಷಗಳು
1. ವೆಲ್ಡಿಂಗ್ ಸರಂಧ್ರತೆ
ಲೇಸರ್ ವೆಲ್ಡಿಂಗ್ನಲ್ಲಿನ ಸಾಮಾನ್ಯ ದೋಷಗಳು ರಂಧ್ರಗಳಾಗಿವೆ.ವೆಲ್ಡಿಂಗ್ ಕರಗಿದ ಪೂಲ್ ಆಳವಾದ ಮತ್ತು ಕಿರಿದಾಗಿದೆ.ಲೇಸರ್ ವೆಲ್ಡಿಂಗ್ ಪ್ರಕ್ರಿಯೆಯಲ್ಲಿ, ಸಾರಜನಕವು ಹೊರಗಿನಿಂದ ಕರಗಿದ ಕೊಳವನ್ನು ಆಕ್ರಮಿಸುತ್ತದೆ.ಲೋಹದ ತಂಪಾಗಿಸುವಿಕೆ ಮತ್ತು ಘನೀಕರಣ ಪ್ರಕ್ರಿಯೆಯಲ್ಲಿ, ತಾಪಮಾನದ ಇಳಿಕೆಯೊಂದಿಗೆ ಸಾರಜನಕದ ಕರಗುವಿಕೆ ಕಡಿಮೆಯಾಗುತ್ತದೆ.ಕರಗಿದ ಪೂಲ್ ಲೋಹವು ಸ್ಫಟಿಕೀಕರಣಗೊಳ್ಳಲು ತಣ್ಣಗಾದಾಗ, ಕರಗುವಿಕೆ ತೀವ್ರವಾಗಿ ಮತ್ತು ಹಠಾತ್ತನೆ ಕುಸಿಯುತ್ತದೆ.ಈ ಸಮಯದಲ್ಲಿ, ದೊಡ್ಡ ಪ್ರಮಾಣದ ಅನಿಲವು ಗುಳ್ಳೆಗಳನ್ನು ರೂಪಿಸಲು ಅವಕ್ಷೇಪಿಸುತ್ತದೆ.ಗುಳ್ಳೆಗಳ ತೇಲುವ ವೇಗವು ಲೋಹದ ಸ್ಫಟಿಕೀಕರಣದ ವೇಗಕ್ಕಿಂತ ಕಡಿಮೆಯಿದ್ದರೆ, ರಂಧ್ರಗಳು ಉತ್ಪತ್ತಿಯಾಗುತ್ತವೆ.
ಲಿಥಿಯಂ ಬ್ಯಾಟರಿ ಉದ್ಯಮದಲ್ಲಿನ ಅನ್ವಯಗಳಲ್ಲಿ, ಧನಾತ್ಮಕ ವಿದ್ಯುದ್ವಾರದ ಬೆಸುಗೆ ಸಮಯದಲ್ಲಿ ರಂಧ್ರಗಳು ವಿಶೇಷವಾಗಿ ಸಂಭವಿಸುವ ಸಾಧ್ಯತೆಯಿದೆ ಎಂದು ನಾವು ಸಾಮಾನ್ಯವಾಗಿ ಕಂಡುಕೊಳ್ಳುತ್ತೇವೆ, ಆದರೆ ನಕಾರಾತ್ಮಕ ವಿದ್ಯುದ್ವಾರದ ಬೆಸುಗೆ ಸಮಯದಲ್ಲಿ ಅಪರೂಪವಾಗಿ ಸಂಭವಿಸುತ್ತದೆ.ಏಕೆಂದರೆ ಧನಾತ್ಮಕ ವಿದ್ಯುದ್ವಾರವು ಅಲ್ಯೂಮಿನಿಯಂನಿಂದ ಮಾಡಲ್ಪಟ್ಟಿದೆ ಮತ್ತು ಋಣಾತ್ಮಕ ವಿದ್ಯುದ್ವಾರವು ತಾಮ್ರದಿಂದ ಮಾಡಲ್ಪಟ್ಟಿದೆ.ವೆಲ್ಡಿಂಗ್ ಸಮಯದಲ್ಲಿ, ಆಂತರಿಕ ಅನಿಲವು ಸಂಪೂರ್ಣವಾಗಿ ಉಕ್ಕಿ ಹರಿಯುವ ಮೊದಲು ಮೇಲ್ಮೈಯಲ್ಲಿರುವ ದ್ರವ ಅಲ್ಯೂಮಿನಿಯಂ ಘನೀಕರಣಗೊಳ್ಳುತ್ತದೆ, ಅನಿಲವು ಉಕ್ಕಿ ಹರಿಯುವುದನ್ನು ತಡೆಯುತ್ತದೆ ಮತ್ತು ದೊಡ್ಡ ಮತ್ತು ಸಣ್ಣ ರಂಧ್ರಗಳನ್ನು ರೂಪಿಸುತ್ತದೆ.ಸಣ್ಣ ಸ್ಟೊಮಾಟಾ.
ಮೇಲೆ ತಿಳಿಸಿದ ರಂಧ್ರಗಳ ಕಾರಣಗಳ ಜೊತೆಗೆ, ರಂಧ್ರಗಳು ಹೊರಾಂಗಣ ಗಾಳಿ, ತೇವಾಂಶ, ಮೇಲ್ಮೈ ತೈಲ ಇತ್ಯಾದಿಗಳನ್ನು ಸಹ ಒಳಗೊಂಡಿರುತ್ತವೆ. ಜೊತೆಗೆ, ಸಾರಜನಕ ಊದುವಿಕೆಯ ದಿಕ್ಕು ಮತ್ತು ಕೋನವು ರಂಧ್ರಗಳ ರಚನೆಯ ಮೇಲೆ ಪರಿಣಾಮ ಬೀರುತ್ತದೆ.
ವೆಲ್ಡಿಂಗ್ ರಂಧ್ರಗಳ ಸಂಭವವನ್ನು ಕಡಿಮೆ ಮಾಡುವುದು ಹೇಗೆ?
ಮೊದಲನೆಯದಾಗಿ, ವೆಲ್ಡಿಂಗ್ ಮಾಡುವ ಮೊದಲು, ಒಳಬರುವ ವಸ್ತುಗಳ ಮೇಲ್ಮೈಯಲ್ಲಿ ತೈಲ ಕಲೆಗಳು ಮತ್ತು ಕಲ್ಮಶಗಳನ್ನು ಸಮಯಕ್ಕೆ ಸ್ವಚ್ಛಗೊಳಿಸಬೇಕಾಗಿದೆ;ಲಿಥಿಯಂ ಬ್ಯಾಟರಿಗಳ ಉತ್ಪಾದನೆಯಲ್ಲಿ, ಒಳಬರುವ ವಸ್ತು ತಪಾಸಣೆ ಅತ್ಯಗತ್ಯ ಪ್ರಕ್ರಿಯೆಯಾಗಿದೆ.
ಎರಡನೆಯದಾಗಿ, ರಕ್ಷಾಕವಚದ ಅನಿಲದ ಹರಿವನ್ನು ಬೆಸುಗೆ ಹಾಕುವ ವೇಗ, ಶಕ್ತಿ, ಸ್ಥಾನ, ಇತ್ಯಾದಿ ಅಂಶಗಳ ಪ್ರಕಾರ ಸರಿಹೊಂದಿಸಬೇಕು ಮತ್ತು ತುಂಬಾ ದೊಡ್ಡದಾಗಿರಬಾರದು ಅಥವಾ ಚಿಕ್ಕದಾಗಿರಬಾರದು.ಲೇಸರ್ ಶಕ್ತಿ ಮತ್ತು ಫೋಕಸ್ ಸ್ಥಾನದಂತಹ ಅಂಶಗಳ ಪ್ರಕಾರ ರಕ್ಷಣಾತ್ಮಕ ಗಡಿಯಾರದ ಒತ್ತಡವನ್ನು ಸರಿಹೊಂದಿಸಬೇಕು ಮತ್ತು ತುಂಬಾ ಹೆಚ್ಚು ಅಥವಾ ತುಂಬಾ ಕಡಿಮೆ ಇರಬಾರದು.ರಕ್ಷಣಾತ್ಮಕ ಗಡಿಯಾರದ ನಳಿಕೆಯ ಆಕಾರವನ್ನು ಆಕಾರ, ದಿಕ್ಕು ಮತ್ತು ವೆಲ್ಡ್ನ ಇತರ ಅಂಶಗಳಿಗೆ ಅನುಗುಣವಾಗಿ ಸರಿಹೊಂದಿಸಬೇಕು ಇದರಿಂದ ರಕ್ಷಣಾತ್ಮಕ ಗಡಿಯಾರವು ವೆಲ್ಡಿಂಗ್ ಪ್ರದೇಶವನ್ನು ಸಮವಾಗಿ ಆವರಿಸುತ್ತದೆ.
ಮೂರನೆಯದಾಗಿ, ಕಾರ್ಯಾಗಾರದಲ್ಲಿ ಗಾಳಿಯಲ್ಲಿ ತಾಪಮಾನ, ಆರ್ದ್ರತೆ ಮತ್ತು ಧೂಳನ್ನು ನಿಯಂತ್ರಿಸಿ.ಸುತ್ತುವರಿದ ತಾಪಮಾನ ಮತ್ತು ತೇವಾಂಶವು ತಲಾಧಾರದ ಮೇಲ್ಮೈ ಮತ್ತು ರಕ್ಷಣಾತ್ಮಕ ಅನಿಲದ ತೇವಾಂಶದ ಮೇಲೆ ಪರಿಣಾಮ ಬೀರುತ್ತದೆ, ಇದು ಕರಗಿದ ಕೊಳದಲ್ಲಿ ನೀರಿನ ಆವಿಯ ಉತ್ಪಾದನೆ ಮತ್ತು ತಪ್ಪಿಸಿಕೊಳ್ಳುವಿಕೆಯ ಮೇಲೆ ಪರಿಣಾಮ ಬೀರುತ್ತದೆ.ಸುತ್ತುವರಿದ ತಾಪಮಾನ ಮತ್ತು ತೇವಾಂಶವು ತುಂಬಾ ಹೆಚ್ಚಿದ್ದರೆ, ತಲಾಧಾರ ಮತ್ತು ರಕ್ಷಣಾತ್ಮಕ ಅನಿಲದ ಮೇಲ್ಮೈಯಲ್ಲಿ ಹೆಚ್ಚಿನ ತೇವಾಂಶ ಇರುತ್ತದೆ, ಇದು ದೊಡ್ಡ ಪ್ರಮಾಣದ ನೀರಿನ ಆವಿಯನ್ನು ಉತ್ಪಾದಿಸುತ್ತದೆ, ಇದರಿಂದಾಗಿ ರಂಧ್ರಗಳು ಉಂಟಾಗುತ್ತವೆ.ಸುತ್ತುವರಿದ ತಾಪಮಾನ ಮತ್ತು ತೇವಾಂಶವು ತುಂಬಾ ಕಡಿಮೆಯಿದ್ದರೆ, ತಲಾಧಾರದ ಮೇಲ್ಮೈಯಲ್ಲಿ ಮತ್ತು ರಕ್ಷಾಕವಚದ ಅನಿಲದಲ್ಲಿ ತುಂಬಾ ಕಡಿಮೆ ತೇವಾಂಶವಿರುತ್ತದೆ, ನೀರಿನ ಆವಿಯ ಉತ್ಪಾದನೆಯನ್ನು ಕಡಿಮೆ ಮಾಡುತ್ತದೆ, ಇದರಿಂದಾಗಿ ರಂಧ್ರಗಳನ್ನು ಕಡಿಮೆ ಮಾಡುತ್ತದೆ;ವೆಲ್ಡಿಂಗ್ ಸ್ಟೇಷನ್ನಲ್ಲಿ ತಾಪಮಾನ, ಆರ್ದ್ರತೆ ಮತ್ತು ಧೂಳಿನ ಗುರಿ ಮೌಲ್ಯವನ್ನು ಗುಣಮಟ್ಟದ ಸಿಬ್ಬಂದಿ ಪತ್ತೆ ಮಾಡಲಿ.
ನಾಲ್ಕನೆಯದಾಗಿ, ಕಿರಣದ ಸ್ವಿಂಗ್ ವಿಧಾನವನ್ನು ಲೇಸರ್ ಆಳವಾದ ನುಗ್ಗುವ ವೆಲ್ಡಿಂಗ್ನಲ್ಲಿ ರಂಧ್ರಗಳನ್ನು ಕಡಿಮೆ ಮಾಡಲು ಅಥವಾ ತೆಗೆದುಹಾಕಲು ಬಳಸಲಾಗುತ್ತದೆ.ವೆಲ್ಡಿಂಗ್ ಸಮಯದಲ್ಲಿ ಸ್ವಿಂಗ್ ಅನ್ನು ಸೇರಿಸುವುದರಿಂದ, ವೆಲ್ಡ್ ಸೀಮ್ಗೆ ಕಿರಣದ ಪರಸ್ಪರ ಸ್ವಿಂಗ್ ವೆಲ್ಡ್ ಸೀಮ್ನ ಭಾಗವನ್ನು ಪುನರಾವರ್ತಿತವಾಗಿ ಮರುಹೊಂದಿಸಲು ಕಾರಣವಾಗುತ್ತದೆ, ಇದು ವೆಲ್ಡಿಂಗ್ ಪೂಲ್ನಲ್ಲಿ ದ್ರವ ಲೋಹದ ನಿವಾಸದ ಸಮಯವನ್ನು ಹೆಚ್ಚಿಸುತ್ತದೆ.ಅದೇ ಸಮಯದಲ್ಲಿ, ಕಿರಣದ ವಿಚಲನವು ಪ್ರತಿ ಯೂನಿಟ್ ಪ್ರದೇಶಕ್ಕೆ ಶಾಖದ ಇನ್ಪುಟ್ ಅನ್ನು ಹೆಚ್ಚಿಸುತ್ತದೆ.ವೆಲ್ಡ್ನ ಆಳ-ಅಗಲ ಅನುಪಾತವು ಕಡಿಮೆಯಾಗುತ್ತದೆ, ಇದು ಗುಳ್ಳೆಗಳ ಹೊರಹೊಮ್ಮುವಿಕೆಗೆ ಅನುಕೂಲಕರವಾಗಿದೆ, ಇದರಿಂದಾಗಿ ರಂಧ್ರಗಳನ್ನು ತೆಗೆದುಹಾಕುತ್ತದೆ.ಮತ್ತೊಂದೆಡೆ, ಕಿರಣದ ಸ್ವಿಂಗ್ ಸಣ್ಣ ರಂಧ್ರಕ್ಕೆ ಅನುಗುಣವಾಗಿ ಸ್ವಿಂಗ್ ಮಾಡಲು ಕಾರಣವಾಗುತ್ತದೆ, ಇದು ವೆಲ್ಡಿಂಗ್ ಪೂಲ್ಗೆ ಸ್ಫೂರ್ತಿದಾಯಕ ಶಕ್ತಿಯನ್ನು ಒದಗಿಸುತ್ತದೆ, ವೆಲ್ಡಿಂಗ್ ಪೂಲ್ನ ಸಂವಹನ ಮತ್ತು ಸ್ಫೂರ್ತಿದಾಯಕವನ್ನು ಹೆಚ್ಚಿಸುತ್ತದೆ ಮತ್ತು ರಂಧ್ರಗಳನ್ನು ತೆಗೆದುಹಾಕುವಲ್ಲಿ ಪ್ರಯೋಜನಕಾರಿ ಪರಿಣಾಮವನ್ನು ಬೀರುತ್ತದೆ.
ಐದನೆಯದಾಗಿ, ನಾಡಿ ಆವರ್ತನ, ನಾಡಿ ಆವರ್ತನವು ಪ್ರತಿ ಯೂನಿಟ್ ಸಮಯಕ್ಕೆ ಲೇಸರ್ ಕಿರಣದಿಂದ ಹೊರಸೂಸುವ ಕಾಳುಗಳ ಸಂಖ್ಯೆಯನ್ನು ಸೂಚಿಸುತ್ತದೆ, ಇದು ಕರಗಿದ ಕೊಳದಲ್ಲಿ ಶಾಖದ ಒಳಹರಿವು ಮತ್ತು ಶಾಖದ ಶೇಖರಣೆಯ ಮೇಲೆ ಪರಿಣಾಮ ಬೀರುತ್ತದೆ ಮತ್ತು ನಂತರ ಕರಗಿದ ತಾಪಮಾನ ಕ್ಷೇತ್ರ ಮತ್ತು ಹರಿವಿನ ಕ್ಷೇತ್ರದ ಮೇಲೆ ಪರಿಣಾಮ ಬೀರುತ್ತದೆ. ಕೊಳ.ನಾಡಿ ಆವರ್ತನವು ತುಂಬಾ ಹೆಚ್ಚಿದ್ದರೆ, ಅದು ಕರಗಿದ ಕೊಳದಲ್ಲಿ ಅತಿಯಾದ ಶಾಖದ ಒಳಹರಿವಿಗೆ ಕಾರಣವಾಗುತ್ತದೆ, ಕರಗಿದ ಕೊಳದ ಉಷ್ಣತೆಯು ತುಂಬಾ ಹೆಚ್ಚಾಗಿರುತ್ತದೆ, ಲೋಹದ ಆವಿ ಅಥವಾ ಹೆಚ್ಚಿನ ತಾಪಮಾನದಲ್ಲಿ ಬಾಷ್ಪಶೀಲವಾಗಿರುವ ಇತರ ಅಂಶಗಳನ್ನು ಉತ್ಪಾದಿಸುತ್ತದೆ, ಇದರಿಂದಾಗಿ ರಂಧ್ರಗಳು ಉಂಟಾಗುತ್ತವೆ.ನಾಡಿ ಆವರ್ತನವು ತುಂಬಾ ಕಡಿಮೆಯಿದ್ದರೆ, ಕರಗಿದ ಕೊಳದಲ್ಲಿ ಸಾಕಷ್ಟು ಶಾಖದ ಶೇಖರಣೆಗೆ ಕಾರಣವಾಗುತ್ತದೆ, ಕರಗಿದ ಕೊಳದ ಉಷ್ಣತೆಯು ತುಂಬಾ ಕಡಿಮೆಯಾಗಿದೆ, ಅನಿಲದ ಕರಗುವಿಕೆ ಮತ್ತು ತಪ್ಪಿಸಿಕೊಳ್ಳುವಿಕೆಯನ್ನು ಕಡಿಮೆ ಮಾಡುತ್ತದೆ, ಇದರಿಂದಾಗಿ ರಂಧ್ರಗಳು ಉಂಟಾಗುತ್ತವೆ.ಸಾಮಾನ್ಯವಾಗಿ ಹೇಳುವುದಾದರೆ, ನಾಡಿ ಆವರ್ತನವನ್ನು ತಲಾಧಾರದ ದಪ್ಪ ಮತ್ತು ಲೇಸರ್ ಶಕ್ತಿಯ ಆಧಾರದ ಮೇಲೆ ಸಮಂಜಸವಾದ ವ್ಯಾಪ್ತಿಯಲ್ಲಿ ಆಯ್ಕೆ ಮಾಡಬೇಕು ಮತ್ತು ತುಂಬಾ ಹೆಚ್ಚು ಅಥವಾ ತುಂಬಾ ಕಡಿಮೆ ಇರುವುದನ್ನು ತಪ್ಪಿಸಬೇಕು.
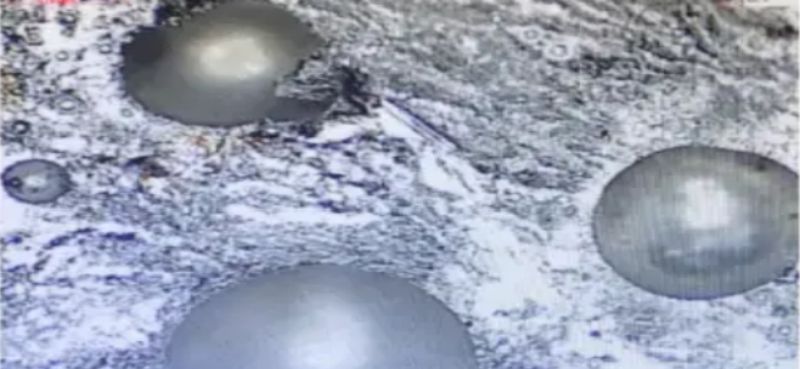
ವೆಲ್ಡಿಂಗ್ ರಂಧ್ರಗಳು (ಲೇಸರ್ ವೆಲ್ಡಿಂಗ್)
2. ವೆಲ್ಡ್ ಸ್ಪಾಟರ್
ವೆಲ್ಡಿಂಗ್ ಪ್ರಕ್ರಿಯೆಯಲ್ಲಿ ಉತ್ಪತ್ತಿಯಾಗುವ ಸ್ಪಟರ್, ಲೇಸರ್ ವೆಲ್ಡಿಂಗ್ ವೆಲ್ಡ್ನ ಮೇಲ್ಮೈ ಗುಣಮಟ್ಟವನ್ನು ಗಂಭೀರವಾಗಿ ಪರಿಣಾಮ ಬೀರುತ್ತದೆ ಮತ್ತು ಮಸೂರವನ್ನು ಮಾಲಿನ್ಯಗೊಳಿಸುತ್ತದೆ ಮತ್ತು ಹಾನಿಗೊಳಿಸುತ್ತದೆ.ಸಾಮಾನ್ಯ ಕಾರ್ಯಕ್ಷಮತೆ ಹೀಗಿದೆ: ಲೇಸರ್ ವೆಲ್ಡಿಂಗ್ ಪೂರ್ಣಗೊಂಡ ನಂತರ, ವಸ್ತು ಅಥವಾ ವರ್ಕ್ಪೀಸ್ನ ಮೇಲ್ಮೈಯಲ್ಲಿ ಅನೇಕ ಲೋಹದ ಕಣಗಳು ಕಾಣಿಸಿಕೊಳ್ಳುತ್ತವೆ ಮತ್ತು ವಸ್ತು ಅಥವಾ ವರ್ಕ್ಪೀಸ್ನ ಮೇಲ್ಮೈಗೆ ಅಂಟಿಕೊಳ್ಳುತ್ತವೆ.ಗ್ಯಾಲ್ವನೋಮೀಟರ್ನ ಮೋಡ್ನಲ್ಲಿ ವೆಲ್ಡಿಂಗ್ ಮಾಡುವಾಗ, ಗ್ಯಾಲ್ವನೋಮೀಟರ್ನ ರಕ್ಷಣಾತ್ಮಕ ಮಸೂರದ ಬಳಕೆಯ ಅವಧಿಯ ನಂತರ, ಮೇಲ್ಮೈಯಲ್ಲಿ ದಟ್ಟವಾದ ಹೊಂಡಗಳಿರುತ್ತವೆ ಮತ್ತು ಈ ಹೊಂಡಗಳು ವೆಲ್ಡಿಂಗ್ ಸ್ಪ್ಯಾಟರ್ನಿಂದ ಉಂಟಾಗುತ್ತವೆ ಎಂಬುದು ಅತ್ಯಂತ ಅರ್ಥಗರ್ಭಿತ ಕಾರ್ಯಕ್ಷಮತೆಯಾಗಿದೆ.ಬಹಳ ಸಮಯದ ನಂತರ, ಬೆಳಕನ್ನು ನಿರ್ಬಂಧಿಸುವುದು ಸುಲಭ, ಮತ್ತು ಬೆಸುಗೆ ಹಾಕುವ ಬೆಳಕಿನಲ್ಲಿ ಸಮಸ್ಯೆಗಳಿರುತ್ತವೆ, ಇದರ ಪರಿಣಾಮವಾಗಿ ಮುರಿದ ಬೆಸುಗೆ ಮತ್ತು ವರ್ಚುವಲ್ ವೆಲ್ಡಿಂಗ್ನಂತಹ ಸಮಸ್ಯೆಗಳ ಸರಣಿ ಉಂಟಾಗುತ್ತದೆ.
ಸ್ಪ್ಲಾಶಿಂಗ್ ಕಾರಣಗಳು ಯಾವುವು?
ಮೊದಲನೆಯದಾಗಿ, ವಿದ್ಯುತ್ ಸಾಂದ್ರತೆ, ಹೆಚ್ಚಿನ ಶಕ್ತಿಯ ಸಾಂದ್ರತೆ, ಸ್ಪ್ಯಾಟರ್ ಅನ್ನು ಉತ್ಪಾದಿಸುವುದು ಸುಲಭ, ಮತ್ತು ಸ್ಪ್ಯಾಟರ್ ನೇರವಾಗಿ ವಿದ್ಯುತ್ ಸಾಂದ್ರತೆಗೆ ಸಂಬಂಧಿಸಿದೆ.ಇದು ಶತಮಾನದಷ್ಟು ಹಳೆಯ ಸಮಸ್ಯೆ.ಕನಿಷ್ಠ ಇಲ್ಲಿಯವರೆಗೆ, ಉದ್ಯಮವು ಸ್ಪ್ಲಾಶಿಂಗ್ ಸಮಸ್ಯೆಯನ್ನು ಪರಿಹರಿಸಲು ಸಾಧ್ಯವಾಗಲಿಲ್ಲ, ಮತ್ತು ಸ್ವಲ್ಪ ಕಡಿಮೆಯಾಗಿದೆ ಎಂದು ಮಾತ್ರ ಹೇಳಬಹುದು.ಲಿಥಿಯಂ ಬ್ಯಾಟರಿ ಉದ್ಯಮದಲ್ಲಿ, ಸ್ಪ್ಲಾಶಿಂಗ್ ಬ್ಯಾಟರಿ ಶಾರ್ಟ್ ಸರ್ಕ್ಯೂಟ್ನ ಅತಿದೊಡ್ಡ ಅಪರಾಧಿಯಾಗಿದೆ, ಆದರೆ ಇದು ಮೂಲ ಕಾರಣವನ್ನು ಪರಿಹರಿಸಲು ಸಾಧ್ಯವಾಗಲಿಲ್ಲ.ಬ್ಯಾಟರಿಯ ಮೇಲೆ ಸ್ಪಾಟರ್ನ ಪ್ರಭಾವವನ್ನು ರಕ್ಷಣೆಯ ದೃಷ್ಟಿಕೋನದಿಂದ ಮಾತ್ರ ಕಡಿಮೆ ಮಾಡಬಹುದು.ಉದಾಹರಣೆಗೆ, ಧೂಳು ತೆಗೆಯುವ ಪೋರ್ಟ್ಗಳು ಮತ್ತು ರಕ್ಷಣಾತ್ಮಕ ಕವರ್ಗಳ ವೃತ್ತವನ್ನು ಬೆಸುಗೆ ಹಾಕುವ ಭಾಗದ ಸುತ್ತಲೂ ಸೇರಿಸಲಾಗುತ್ತದೆ ಮತ್ತು ಸ್ಪಟರ್ನ ಪ್ರಭಾವವನ್ನು ತಡೆಯಲು ಅಥವಾ ಬ್ಯಾಟರಿಗೆ ಹಾನಿಯಾಗದಂತೆ ಏರ್ ಚಾಕುಗಳ ಸಾಲುಗಳನ್ನು ವಲಯಗಳಲ್ಲಿ ಸೇರಿಸಲಾಗುತ್ತದೆ.ವೆಲ್ಡಿಂಗ್ ಸ್ಟೇಷನ್ ಸುತ್ತಲಿನ ಪರಿಸರ, ಉತ್ಪನ್ನಗಳು ಮತ್ತು ಘಟಕಗಳನ್ನು ನಾಶಮಾಡುವುದು ಎಂದರೆ ದಣಿದಿದೆ ಎಂದು ಹೇಳಬಹುದು.
ಸ್ಪ್ಯಾಟರ್ ಸಮಸ್ಯೆಯನ್ನು ಪರಿಹರಿಸಲು, ವೆಲ್ಡಿಂಗ್ ಶಕ್ತಿಯನ್ನು ಕಡಿಮೆ ಮಾಡುವುದು ಸ್ಪ್ಯಾಟರ್ ಅನ್ನು ಕಡಿಮೆ ಮಾಡಲು ಸಹಾಯ ಮಾಡುತ್ತದೆ ಎಂದು ಮಾತ್ರ ಹೇಳಬಹುದು.ಒಳಹೊಕ್ಕು ಸಾಕಷ್ಟಿಲ್ಲದಿದ್ದರೆ ವೆಲ್ಡಿಂಗ್ ವೇಗವನ್ನು ಕಡಿಮೆ ಮಾಡುವುದು ಸಹ ಸಹಾಯ ಮಾಡುತ್ತದೆ.ಆದರೆ ಕೆಲವು ವಿಶೇಷ ಪ್ರಕ್ರಿಯೆ ಅಗತ್ಯತೆಗಳಲ್ಲಿ, ಇದು ಕಡಿಮೆ ಪರಿಣಾಮವನ್ನು ಬೀರುತ್ತದೆ.ಇದು ಒಂದೇ ಪ್ರಕ್ರಿಯೆಯಾಗಿದೆ, ವಿಭಿನ್ನ ಯಂತ್ರಗಳು ಮತ್ತು ವಸ್ತುಗಳ ವಿವಿಧ ಬ್ಯಾಚ್ಗಳು ಸಂಪೂರ್ಣವಾಗಿ ವಿಭಿನ್ನ ವೆಲ್ಡಿಂಗ್ ಪರಿಣಾಮಗಳನ್ನು ಹೊಂದಿವೆ.ಆದ್ದರಿಂದ, ಹೊಸ ಶಕ್ತಿ ಉದ್ಯಮದಲ್ಲಿ ಒಂದು ಅಲಿಖಿತ ನಿಯಮವಿದೆ, ಒಂದು ತುಂಡು ಉಪಕರಣಕ್ಕಾಗಿ ವೆಲ್ಡಿಂಗ್ ನಿಯತಾಂಕಗಳ ಒಂದು ಸೆಟ್.
ಎರಡನೆಯದಾಗಿ, ಸಂಸ್ಕರಿಸಿದ ವಸ್ತು ಅಥವಾ ವರ್ಕ್ಪೀಸ್ನ ಮೇಲ್ಮೈಯನ್ನು ಸ್ವಚ್ಛಗೊಳಿಸದಿದ್ದರೆ, ತೈಲ ಕಲೆಗಳು ಅಥವಾ ಮಾಲಿನ್ಯಕಾರಕಗಳು ಸಹ ಗಂಭೀರ ಸ್ಪ್ಲಾಶ್ಗಳನ್ನು ಉಂಟುಮಾಡುತ್ತವೆ.ಈ ಸಮಯದಲ್ಲಿ, ಸಂಸ್ಕರಿಸಿದ ವಸ್ತುಗಳ ಮೇಲ್ಮೈಯನ್ನು ಸ್ವಚ್ಛಗೊಳಿಸಲು ಸುಲಭವಾದ ವಿಷಯವಾಗಿದೆ.
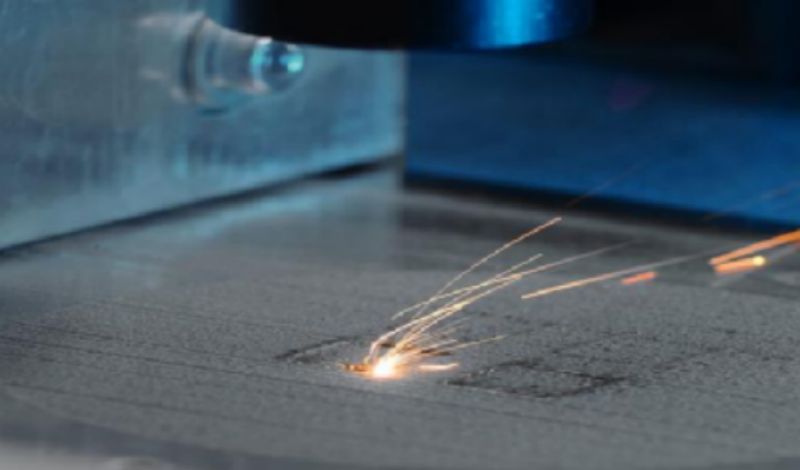
3. ಲೇಸರ್ ವೆಲ್ಡಿಂಗ್ನ ಹೆಚ್ಚಿನ ಪ್ರತಿಫಲನ
ಸಾಮಾನ್ಯವಾಗಿ ಹೇಳುವುದಾದರೆ, ಹೆಚ್ಚಿನ ಪ್ರತಿಫಲನವು ಸಂಸ್ಕರಣಾ ವಸ್ತುವು ಸಣ್ಣ ಪ್ರತಿರೋಧಕತೆ, ತುಲನಾತ್ಮಕವಾಗಿ ನಯವಾದ ಮೇಲ್ಮೈ ಮತ್ತು ಅತಿಗೆಂಪು ಲೇಸರ್ಗಳಿಗೆ ಕಡಿಮೆ ಹೀರಿಕೊಳ್ಳುವ ದರವನ್ನು ಹೊಂದಿದೆ, ಇದು ಹೆಚ್ಚಿನ ಪ್ರಮಾಣದ ಲೇಸರ್ ಹೊರಸೂಸುವಿಕೆಗೆ ಕಾರಣವಾಗುತ್ತದೆ ಮತ್ತು ಹೆಚ್ಚಿನ ಲೇಸರ್ಗಳನ್ನು ಬಳಸಲಾಗುತ್ತದೆ. ವಸ್ತು ಅಥವಾ ಸಣ್ಣ ಪ್ರಮಾಣದ ಇಳಿಜಾರಿನ ಕಾರಣದಿಂದಾಗಿ ಲಂಬವಾಗಿ, ಹಿಂತಿರುಗುವ ಲೇಸರ್ ಬೆಳಕು ಔಟ್ಪುಟ್ ಹೆಡ್ಗೆ ಮರು-ಪ್ರವೇಶಿಸುತ್ತದೆ, ಮತ್ತು ಹಿಂತಿರುಗುವ ಬೆಳಕಿನ ಭಾಗವು ಶಕ್ತಿ-ಹರಡುವ ಫೈಬರ್ಗೆ ಸೇರಿಕೊಳ್ಳುತ್ತದೆ ಮತ್ತು ಫೈಬರ್ನ ಉದ್ದಕ್ಕೂ ಒಳಭಾಗಕ್ಕೆ ಹರಡುತ್ತದೆ ಲೇಸರ್ನ, ಲೇಸರ್ನೊಳಗಿನ ಕೋರ್ ಘಟಕಗಳು ಹೆಚ್ಚಿನ ತಾಪಮಾನದಲ್ಲಿ ಮುಂದುವರಿಯುವಂತೆ ಮಾಡುತ್ತದೆ.
ಲೇಸರ್ ವೆಲ್ಡಿಂಗ್ ಸಮಯದಲ್ಲಿ ಪ್ರತಿಫಲನವು ತುಂಬಾ ಹೆಚ್ಚಾದಾಗ, ಈ ಕೆಳಗಿನ ಪರಿಹಾರಗಳನ್ನು ತೆಗೆದುಕೊಳ್ಳಬಹುದು:
3.1 ವಿರೋಧಿ ಪ್ರತಿಫಲಿತ ಲೇಪನವನ್ನು ಬಳಸಿ ಅಥವಾ ವಸ್ತುವಿನ ಮೇಲ್ಮೈಗೆ ಚಿಕಿತ್ಸೆ ನೀಡಿ: ವೆಲ್ಡಿಂಗ್ ವಸ್ತುವಿನ ಮೇಲ್ಮೈಯನ್ನು ವಿರೋಧಿ ಪ್ರತಿಫಲಿತ ಲೇಪನದೊಂದಿಗೆ ಲೇಸರ್ ಲೇಸರ್ನ ಪ್ರತಿಫಲನವನ್ನು ಪರಿಣಾಮಕಾರಿಯಾಗಿ ಕಡಿಮೆ ಮಾಡುತ್ತದೆ.ಈ ಲೇಪನವು ಸಾಮಾನ್ಯವಾಗಿ ಕಡಿಮೆ ಪ್ರತಿಫಲನವನ್ನು ಹೊಂದಿರುವ ವಿಶೇಷ ಆಪ್ಟಿಕಲ್ ವಸ್ತುವಾಗಿದ್ದು, ಅದನ್ನು ಪ್ರತಿಬಿಂಬಿಸುವ ಬದಲು ಲೇಸರ್ ಶಕ್ತಿಯನ್ನು ಹೀರಿಕೊಳ್ಳುತ್ತದೆ.ಪ್ರಸ್ತುತ ಸಂಗ್ರಾಹಕ ವೆಲ್ಡಿಂಗ್, ಮೃದು ಸಂಪರ್ಕ, ಇತ್ಯಾದಿಗಳಂತಹ ಕೆಲವು ಪ್ರಕ್ರಿಯೆಗಳಲ್ಲಿ, ಮೇಲ್ಮೈಯನ್ನು ಕೂಡ ಉಬ್ಬು ಹಾಕಬಹುದು.
3.2 ವೆಲ್ಡಿಂಗ್ ಕೋನವನ್ನು ಹೊಂದಿಸಿ: ವೆಲ್ಡಿಂಗ್ ಕೋನವನ್ನು ಸರಿಹೊಂದಿಸುವ ಮೂಲಕ, ಲೇಸರ್ ಕಿರಣವು ಹೆಚ್ಚು ಸೂಕ್ತವಾದ ಕೋನದಲ್ಲಿ ವೆಲ್ಡಿಂಗ್ ವಸ್ತುವಿನ ಮೇಲೆ ಸಂಭವಿಸಬಹುದು ಮತ್ತು ಪ್ರತಿಫಲನದ ಸಂಭವವನ್ನು ಕಡಿಮೆ ಮಾಡುತ್ತದೆ.ಸಾಮಾನ್ಯವಾಗಿ, ವೆಲ್ಡ್ ಮಾಡಬೇಕಾದ ವಸ್ತುವಿನ ಮೇಲ್ಮೈಗೆ ಲಂಬವಾಗಿ ಲೇಸರ್ ಕಿರಣದ ಘಟನೆಯು ಪ್ರತಿಫಲನಗಳನ್ನು ಕಡಿಮೆ ಮಾಡಲು ಉತ್ತಮ ಮಾರ್ಗವಾಗಿದೆ.
3.3 ಸಹಾಯಕ ಹೀರಿಕೊಳ್ಳುವಿಕೆಯನ್ನು ಸೇರಿಸುವುದು: ವೆಲ್ಡಿಂಗ್ ಪ್ರಕ್ರಿಯೆಯಲ್ಲಿ, ಪುಡಿ ಅಥವಾ ದ್ರವದಂತಹ ನಿರ್ದಿಷ್ಟ ಪ್ರಮಾಣದ ಸಹಾಯಕ ಹೀರಿಕೊಳ್ಳುವಿಕೆಯನ್ನು ವೆಲ್ಡ್ಗೆ ಸೇರಿಸಲಾಗುತ್ತದೆ.ಈ ಅಬ್ಸಾರ್ಬರ್ಗಳು ಲೇಸರ್ ಶಕ್ತಿಯನ್ನು ಹೀರಿಕೊಳ್ಳುತ್ತವೆ ಮತ್ತು ಪ್ರತಿಫಲನವನ್ನು ಕಡಿಮೆ ಮಾಡುತ್ತದೆ.ನಿರ್ದಿಷ್ಟ ವೆಲ್ಡಿಂಗ್ ವಸ್ತುಗಳು ಮತ್ತು ಅಪ್ಲಿಕೇಶನ್ ಸನ್ನಿವೇಶಗಳ ಆಧಾರದ ಮೇಲೆ ಸೂಕ್ತವಾದ ಹೀರಿಕೊಳ್ಳುವಿಕೆಯನ್ನು ಆಯ್ಕೆ ಮಾಡಬೇಕಾಗುತ್ತದೆ.ಲಿಥಿಯಂ ಬ್ಯಾಟರಿ ಉದ್ಯಮದಲ್ಲಿ, ಇದು ಅಸಂಭವವಾಗಿದೆ.
3.4 ಲೇಸರ್ ಅನ್ನು ರವಾನಿಸಲು ಆಪ್ಟಿಕಲ್ ಫೈಬರ್ ಅನ್ನು ಬಳಸಿ: ಸಾಧ್ಯವಾದರೆ, ಪ್ರತಿಫಲಿತತೆಯನ್ನು ಕಡಿಮೆ ಮಾಡಲು ವೆಲ್ಡಿಂಗ್ ಸ್ಥಾನಕ್ಕೆ ಲೇಸರ್ ಅನ್ನು ರವಾನಿಸಲು ಆಪ್ಟಿಕಲ್ ಫೈಬರ್ ಅನ್ನು ಬಳಸಬಹುದು.ಆಪ್ಟಿಕಲ್ ಫೈಬರ್ಗಳು ವೆಲ್ಡಿಂಗ್ ವಸ್ತುವಿನ ಮೇಲ್ಮೈಗೆ ನೇರವಾಗಿ ಒಡ್ಡಿಕೊಳ್ಳುವುದನ್ನು ತಪ್ಪಿಸಲು ಮತ್ತು ಪ್ರತಿಫಲನಗಳ ಸಂಭವವನ್ನು ಕಡಿಮೆ ಮಾಡಲು ಲೇಸರ್ ಕಿರಣವನ್ನು ವೆಲ್ಡಿಂಗ್ ಪ್ರದೇಶಕ್ಕೆ ಮಾರ್ಗದರ್ಶನ ಮಾಡಬಹುದು.
3.5 ಲೇಸರ್ ನಿಯತಾಂಕಗಳನ್ನು ಹೊಂದಿಸುವುದು: ಲೇಸರ್ ಪವರ್, ಫೋಕಲ್ ಲೆಂತ್ ಮತ್ತು ಫೋಕಲ್ ವ್ಯಾಸದಂತಹ ನಿಯತಾಂಕಗಳನ್ನು ಹೊಂದಿಸುವ ಮೂಲಕ, ಲೇಸರ್ ಶಕ್ತಿಯ ವಿತರಣೆಯನ್ನು ನಿಯಂತ್ರಿಸಬಹುದು ಮತ್ತು ಪ್ರತಿಫಲನಗಳನ್ನು ಕಡಿಮೆ ಮಾಡಬಹುದು.ಕೆಲವು ಪ್ರತಿಫಲಿತ ವಸ್ತುಗಳಿಗೆ, ಲೇಸರ್ ಶಕ್ತಿಯನ್ನು ಕಡಿಮೆ ಮಾಡುವುದು ಪ್ರತಿಫಲನಗಳನ್ನು ಕಡಿಮೆ ಮಾಡಲು ಪರಿಣಾಮಕಾರಿ ಮಾರ್ಗವಾಗಿದೆ.
3.6 ಬೀಮ್ ಸ್ಪ್ಲಿಟರ್ ಅನ್ನು ಬಳಸಿ: ಕಿರಣದ ಸ್ಪ್ಲಿಟರ್ ಲೇಸರ್ ಶಕ್ತಿಯ ಭಾಗವನ್ನು ಹೀರಿಕೊಳ್ಳುವ ಸಾಧನಕ್ಕೆ ಮಾರ್ಗದರ್ಶನ ಮಾಡುತ್ತದೆ, ಇದರಿಂದಾಗಿ ಪ್ರತಿಫಲನಗಳ ಸಂಭವವನ್ನು ಕಡಿಮೆ ಮಾಡುತ್ತದೆ.ಕಿರಣವನ್ನು ವಿಭಜಿಸುವ ಸಾಧನಗಳು ಸಾಮಾನ್ಯವಾಗಿ ಆಪ್ಟಿಕಲ್ ಘಟಕಗಳು ಮತ್ತು ಹೀರಿಕೊಳ್ಳುವವರನ್ನು ಒಳಗೊಂಡಿರುತ್ತವೆ ಮತ್ತು ಸೂಕ್ತವಾದ ಘಟಕಗಳನ್ನು ಆಯ್ಕೆ ಮಾಡುವ ಮೂಲಕ ಮತ್ತು ಸಾಧನದ ವಿನ್ಯಾಸವನ್ನು ಸರಿಹೊಂದಿಸುವ ಮೂಲಕ, ಕಡಿಮೆ ಪ್ರತಿಫಲನವನ್ನು ಸಾಧಿಸಬಹುದು.
4. ವೆಲ್ಡಿಂಗ್ ಅಂಡರ್ಕಟ್
ಲಿಥಿಯಂ ಬ್ಯಾಟರಿ ಉತ್ಪಾದನಾ ಪ್ರಕ್ರಿಯೆಯಲ್ಲಿ, ಯಾವ ಪ್ರಕ್ರಿಯೆಗಳು ಅಂಡರ್ಕಟಿಂಗ್ಗೆ ಕಾರಣವಾಗುತ್ತವೆ?ಅಂಡರ್ಕಟಿಂಗ್ ಏಕೆ ಸಂಭವಿಸುತ್ತದೆ?ಅದನ್ನು ವಿಶ್ಲೇಷಿಸೋಣ.
ಅಂಡರ್ಕಟ್, ಸಾಮಾನ್ಯವಾಗಿ ವೆಲ್ಡಿಂಗ್ ಕಚ್ಚಾ ವಸ್ತುಗಳು ಒಂದಕ್ಕೊಂದು ಚೆನ್ನಾಗಿ ಸಂಯೋಜಿಸಲ್ಪಟ್ಟಿಲ್ಲ, ಅಂತರವು ತುಂಬಾ ದೊಡ್ಡದಾಗಿದೆ ಅಥವಾ ತೋಡು ಕಾಣಿಸಿಕೊಳ್ಳುತ್ತದೆ, ಆಳ ಮತ್ತು ಅಗಲವು ಮೂಲತಃ 0.5mm ಗಿಂತ ಹೆಚ್ಚಾಗಿರುತ್ತದೆ, ಒಟ್ಟು ಉದ್ದವು ವೆಲ್ಡ್ ಉದ್ದದ 10% ಕ್ಕಿಂತ ಹೆಚ್ಚಾಗಿರುತ್ತದೆ ಅಥವಾ ವಿನಂತಿಸಿದ ಉದ್ದದ ಉತ್ಪನ್ನ ಪ್ರಕ್ರಿಯೆ ಮಾನದಂಡಕ್ಕಿಂತ ಹೆಚ್ಚಿನದು.
ಸಂಪೂರ್ಣ ಲಿಥಿಯಂ ಬ್ಯಾಟರಿ ಉತ್ಪಾದನಾ ಪ್ರಕ್ರಿಯೆಯಲ್ಲಿ, ಅಂಡರ್ಕಟಿಂಗ್ ಸಂಭವಿಸುವ ಸಾಧ್ಯತೆ ಹೆಚ್ಚು, ಮತ್ತು ಇದನ್ನು ಸಾಮಾನ್ಯವಾಗಿ ಸಿಲಿಂಡರಾಕಾರದ ಕವರ್ ಪ್ಲೇಟ್ನ ಸೀಲಿಂಗ್ ಪೂರ್ವ-ವೆಲ್ಡಿಂಗ್ ಮತ್ತು ವೆಲ್ಡಿಂಗ್ ಮತ್ತು ಸ್ಕ್ವೇರ್ ಅಲ್ಯೂಮಿನಿಯಂ ಶೆಲ್ ಕವರ್ ಪ್ಲೇಟ್ನ ಸೀಲಿಂಗ್ ಪೂರ್ವ-ವೆಲ್ಡಿಂಗ್ ಮತ್ತು ವೆಲ್ಡಿಂಗ್ನಲ್ಲಿ ವಿತರಿಸಲಾಗುತ್ತದೆ.ಮುಖ್ಯ ಕಾರಣವೆಂದರೆ ಸೀಲಿಂಗ್ ಕವರ್ ಪ್ಲೇಟ್ ವೆಲ್ಡಿಂಗ್ಗೆ ಶೆಲ್ನೊಂದಿಗೆ ಸಹಕರಿಸಬೇಕಾಗುತ್ತದೆ, ಸೀಲಿಂಗ್ ಕವರ್ ಪ್ಲೇಟ್ ಮತ್ತು ಶೆಲ್ ನಡುವಿನ ಹೊಂದಾಣಿಕೆಯ ಪ್ರಕ್ರಿಯೆಯು ಅತಿಯಾದ ವೆಲ್ಡ್ ಅಂತರಗಳು, ಚಡಿಗಳು, ಕುಸಿತ ಇತ್ಯಾದಿಗಳಿಗೆ ಗುರಿಯಾಗುತ್ತದೆ, ಆದ್ದರಿಂದ ಇದು ವಿಶೇಷವಾಗಿ ಅಂಡರ್ಕಟ್ಗಳಿಗೆ ಗುರಿಯಾಗುತ್ತದೆ. .
ಹಾಗಾದರೆ ಕಡಿಮೆಗೊಳಿಸುವಿಕೆಗೆ ಕಾರಣವೇನು?
ವೆಲ್ಡಿಂಗ್ ವೇಗವು ತುಂಬಾ ವೇಗವಾಗಿದ್ದರೆ, ವೆಲ್ಡ್ನ ಮಧ್ಯಭಾಗಕ್ಕೆ ಸೂಚಿಸುವ ಸಣ್ಣ ರಂಧ್ರದ ಹಿಂದೆ ದ್ರವ ಲೋಹವು ಮರುಹಂಚಿಕೆ ಮಾಡಲು ಸಮಯವನ್ನು ಹೊಂದಿರುವುದಿಲ್ಲ, ಇದರ ಪರಿಣಾಮವಾಗಿ ವೆಲ್ಡ್ನ ಎರಡೂ ಬದಿಗಳಲ್ಲಿ ಘನೀಕರಣ ಮತ್ತು ಅಂಡರ್ಕಟಿಂಗ್ ಉಂಟಾಗುತ್ತದೆ.ಮೇಲಿನ ಪರಿಸ್ಥಿತಿಯ ದೃಷ್ಟಿಯಿಂದ, ನಾವು ವೆಲ್ಡಿಂಗ್ ನಿಯತಾಂಕಗಳನ್ನು ಅತ್ಯುತ್ತಮವಾಗಿಸಬೇಕಾಗಿದೆ.ಸರಳವಾಗಿ ಹೇಳುವುದಾದರೆ, ಇದು ವಿವಿಧ ನಿಯತಾಂಕಗಳನ್ನು ಪರಿಶೀಲಿಸಲು ಪುನರಾವರ್ತಿತ ಪ್ರಯೋಗಗಳು ಮತ್ತು ಸೂಕ್ತವಾದ ನಿಯತಾಂಕಗಳು ಕಂಡುಬರುವವರೆಗೆ DOE ಮಾಡುವುದನ್ನು ಮುಂದುವರಿಸಿ.
2. ಬೆಸುಗೆ ಹಾಕುವ ವಸ್ತುಗಳ ಅತಿಯಾದ ವೆಲ್ಡ್ ಅಂತರಗಳು, ಚಡಿಗಳು, ಕುಸಿತಗಳು, ಇತ್ಯಾದಿಗಳು ಕರಗಿದ ಲೋಹದ ಅಂತರವನ್ನು ತುಂಬುವ ಪ್ರಮಾಣವನ್ನು ಕಡಿಮೆ ಮಾಡುತ್ತದೆ, ಇದರಿಂದಾಗಿ ಅಂಡರ್ಕಟ್ಗಳು ಸಂಭವಿಸುವ ಸಾಧ್ಯತೆ ಹೆಚ್ಚು.ಇದು ಉಪಕರಣಗಳು ಮತ್ತು ಕಚ್ಚಾ ವಸ್ತುಗಳ ಪ್ರಶ್ನೆಯಾಗಿದೆ.ವೆಲ್ಡಿಂಗ್ ಕಚ್ಚಾ ವಸ್ತುಗಳು ನಮ್ಮ ಪ್ರಕ್ರಿಯೆಯ ಒಳಬರುವ ವಸ್ತುಗಳ ಅವಶ್ಯಕತೆಗಳನ್ನು ಪೂರೈಸುತ್ತವೆಯೇ, ಸಲಕರಣೆಗಳ ನಿಖರತೆಯು ಅವಶ್ಯಕತೆಗಳನ್ನು ಪೂರೈಸುತ್ತದೆಯೇ, ಇತ್ಯಾದಿ. ಸಾಮಾನ್ಯ ಅಭ್ಯಾಸವು ಪೂರೈಕೆದಾರರು ಮತ್ತು ಸಲಕರಣೆಗಳ ಉಸ್ತುವಾರಿ ಹೊಂದಿರುವ ಜನರನ್ನು ನಿರಂತರವಾಗಿ ಹಿಂಸಿಸುವುದು ಮತ್ತು ಸೋಲಿಸುವುದು.
3. ಲೇಸರ್ ವೆಲ್ಡಿಂಗ್ನ ಕೊನೆಯಲ್ಲಿ ಶಕ್ತಿಯು ತುಂಬಾ ವೇಗವಾಗಿ ಇಳಿದರೆ, ಸಣ್ಣ ರಂಧ್ರವು ಕುಸಿಯಬಹುದು, ಇದು ಸ್ಥಳೀಯ ಅಂಡರ್ಕಟಿಂಗ್ಗೆ ಕಾರಣವಾಗುತ್ತದೆ.ಶಕ್ತಿ ಮತ್ತು ವೇಗದ ಸರಿಯಾದ ಹೊಂದಾಣಿಕೆಯು ಅಂಡರ್ಕಟ್ಗಳ ರಚನೆಯನ್ನು ಪರಿಣಾಮಕಾರಿಯಾಗಿ ತಡೆಯುತ್ತದೆ.ಹಳೆಯ ಮಾತುಗಳಂತೆ, ಪ್ರಯೋಗಗಳನ್ನು ಪುನರಾವರ್ತಿಸಿ, ವಿವಿಧ ನಿಯತಾಂಕಗಳನ್ನು ಪರಿಶೀಲಿಸಿ ಮತ್ತು ನೀವು ಸರಿಯಾದ ನಿಯತಾಂಕಗಳನ್ನು ಕಂಡುಹಿಡಿಯುವವರೆಗೆ DOE ಅನ್ನು ಮುಂದುವರಿಸಿ.
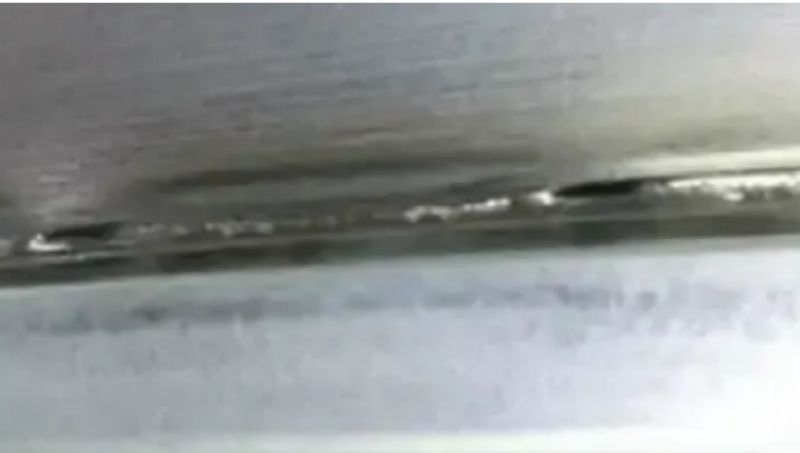
5. ವೆಲ್ಡ್ ಸೆಂಟರ್ ಕುಸಿತ
ವೆಲ್ಡಿಂಗ್ ವೇಗವು ನಿಧಾನವಾಗಿದ್ದರೆ, ಕರಗಿದ ಪೂಲ್ ದೊಡ್ಡದಾಗಿರುತ್ತದೆ ಮತ್ತು ಅಗಲವಾಗಿರುತ್ತದೆ, ಕರಗಿದ ಲೋಹದ ಪ್ರಮಾಣವನ್ನು ಹೆಚ್ಚಿಸುತ್ತದೆ.ಇದು ಮೇಲ್ಮೈ ಒತ್ತಡವನ್ನು ನಿರ್ವಹಿಸುವುದು ಕಷ್ಟಕರವಾಗಿಸುತ್ತದೆ.ಕರಗಿದ ಲೋಹವು ತುಂಬಾ ಭಾರವಾದಾಗ, ವೆಲ್ಡ್ನ ಮಧ್ಯಭಾಗವು ಮುಳುಗಬಹುದು ಮತ್ತು ಅದ್ದುಗಳು ಮತ್ತು ಹೊಂಡಗಳನ್ನು ರೂಪಿಸಬಹುದು.ಈ ಸಂದರ್ಭದಲ್ಲಿ, ಕರಗುವ ಪೂಲ್ ಕುಸಿತವನ್ನು ತಡೆಗಟ್ಟಲು ಶಕ್ತಿಯ ಸಾಂದ್ರತೆಯನ್ನು ಸೂಕ್ತವಾಗಿ ಕಡಿಮೆ ಮಾಡಬೇಕಾಗುತ್ತದೆ.
ಮತ್ತೊಂದು ಪರಿಸ್ಥಿತಿಯಲ್ಲಿ, ವೆಲ್ಡಿಂಗ್ ಅಂತರವು ರಂಧ್ರವನ್ನು ಉಂಟುಮಾಡದೆಯೇ ಕುಸಿತವನ್ನು ರೂಪಿಸುತ್ತದೆ.ಇದು ನಿಸ್ಸಂದೇಹವಾಗಿ ಉಪಕರಣದ ಪ್ರೆಸ್ ಫಿಟ್ನ ಸಮಸ್ಯೆಯಾಗಿದೆ.
ಲೇಸರ್ ವೆಲ್ಡಿಂಗ್ ಸಮಯದಲ್ಲಿ ಸಂಭವಿಸಬಹುದಾದ ದೋಷಗಳು ಮತ್ತು ವಿವಿಧ ದೋಷಗಳ ಕಾರಣಗಳ ಸರಿಯಾದ ತಿಳುವಳಿಕೆಯು ಯಾವುದೇ ಅಸಹಜ ವೆಲ್ಡಿಂಗ್ ಸಮಸ್ಯೆಗಳನ್ನು ಪರಿಹರಿಸಲು ಹೆಚ್ಚು ಉದ್ದೇಶಿತ ವಿಧಾನವನ್ನು ಅನುಮತಿಸುತ್ತದೆ.
6. ವೆಲ್ಡ್ ಬಿರುಕುಗಳು
ನಿರಂತರ ಲೇಸರ್ ವೆಲ್ಡಿಂಗ್ ಸಮಯದಲ್ಲಿ ಕಂಡುಬರುವ ಬಿರುಕುಗಳು ಮುಖ್ಯವಾಗಿ ಉಷ್ಣ ಬಿರುಕುಗಳು, ಉದಾಹರಣೆಗೆ ಸ್ಫಟಿಕ ಬಿರುಕುಗಳು ಮತ್ತು ದ್ರವೀಕರಣ ಬಿರುಕುಗಳು.ಈ ಬಿರುಕುಗಳಿಗೆ ಮುಖ್ಯ ಕಾರಣವೆಂದರೆ ಅದು ಸಂಪೂರ್ಣವಾಗಿ ಘನೀಕರಿಸುವ ಮೊದಲು ವೆಲ್ಡ್ನಿಂದ ಉತ್ಪತ್ತಿಯಾಗುವ ದೊಡ್ಡ ಕುಗ್ಗುವಿಕೆ ಶಕ್ತಿಗಳು.
ಲೇಸರ್ ವೆಲ್ಡಿಂಗ್ನಲ್ಲಿ ಬಿರುಕುಗಳಿಗೆ ಈ ಕೆಳಗಿನ ಕಾರಣಗಳಿವೆ:
1. ಅಸಮಂಜಸವಾದ ವೆಲ್ಡ್ ವಿನ್ಯಾಸ: ಜ್ಯಾಮಿತಿಯ ಅಸಮರ್ಪಕ ವಿನ್ಯಾಸ ಮತ್ತು ವೆಲ್ಡ್ನ ಗಾತ್ರವು ಬೆಸುಗೆ ಒತ್ತಡದ ಸಾಂದ್ರತೆಯನ್ನು ಉಂಟುಮಾಡಬಹುದು, ಇದರಿಂದಾಗಿ ಬಿರುಕುಗಳು ಉಂಟಾಗಬಹುದು.ವೆಲ್ಡಿಂಗ್ ಒತ್ತಡದ ಸಾಂದ್ರತೆಯನ್ನು ತಪ್ಪಿಸಲು ವೆಲ್ಡ್ ವಿನ್ಯಾಸವನ್ನು ಉತ್ತಮಗೊಳಿಸುವುದು ಪರಿಹಾರವಾಗಿದೆ.ನೀವು ಸೂಕ್ತವಾದ ಆಫ್ಸೆಟ್ ವೆಲ್ಡ್ಗಳನ್ನು ಬಳಸಬಹುದು, ವೆಲ್ಡ್ ಆಕಾರವನ್ನು ಬದಲಾಯಿಸಬಹುದು, ಇತ್ಯಾದಿ.
2. ವೆಲ್ಡಿಂಗ್ ನಿಯತಾಂಕಗಳ ಅಸಾಮರಸ್ಯ: ವೆಲ್ಡಿಂಗ್ ಪ್ಯಾರಾಮೀಟರ್ಗಳ ಅಸಮರ್ಪಕ ಆಯ್ಕೆ, ಉದಾಹರಣೆಗೆ ತುಂಬಾ ವೇಗದ ವೆಲ್ಡಿಂಗ್ ವೇಗ, ತುಂಬಾ ಹೆಚ್ಚಿನ ಶಕ್ತಿ, ಇತ್ಯಾದಿ, ವೆಲ್ಡಿಂಗ್ ಪ್ರದೇಶದಲ್ಲಿ ಅಸಮ ತಾಪಮಾನ ಬದಲಾವಣೆಗಳಿಗೆ ಕಾರಣವಾಗಬಹುದು, ಇದು ದೊಡ್ಡ ಬೆಸುಗೆ ಒತ್ತಡ ಮತ್ತು ಬಿರುಕುಗಳಿಗೆ ಕಾರಣವಾಗುತ್ತದೆ.ನಿರ್ದಿಷ್ಟ ವಸ್ತು ಮತ್ತು ವೆಲ್ಡಿಂಗ್ ಪರಿಸ್ಥಿತಿಗಳಿಗೆ ಹೊಂದಿಸಲು ವೆಲ್ಡಿಂಗ್ ನಿಯತಾಂಕಗಳನ್ನು ಸರಿಹೊಂದಿಸುವುದು ಪರಿಹಾರವಾಗಿದೆ.
3. ವೆಲ್ಡಿಂಗ್ ಮೇಲ್ಮೈಯ ಕಳಪೆ ತಯಾರಿಕೆ: ವೆಲ್ಡಿಂಗ್ ಮಾಡುವ ಮೊದಲು ವೆಲ್ಡಿಂಗ್ ಮೇಲ್ಮೈಯನ್ನು ಸರಿಯಾಗಿ ಸ್ವಚ್ಛಗೊಳಿಸಲು ಮತ್ತು ಪೂರ್ವ-ಚಿಕಿತ್ಸೆ ಮಾಡಲು ವಿಫಲವಾದರೆ, ಆಕ್ಸೈಡ್ಗಳು, ಗ್ರೀಸ್, ಇತ್ಯಾದಿಗಳನ್ನು ತೆಗೆದುಹಾಕುವುದು, ವೆಲ್ಡ್ನ ಗುಣಮಟ್ಟ ಮತ್ತು ಬಲದ ಮೇಲೆ ಪರಿಣಾಮ ಬೀರುತ್ತದೆ ಮತ್ತು ಸುಲಭವಾಗಿ ಬಿರುಕುಗಳಿಗೆ ಕಾರಣವಾಗುತ್ತದೆ.ವೆಲ್ಡಿಂಗ್ ಪ್ರದೇಶದಲ್ಲಿನ ಕಲ್ಮಶಗಳು ಮತ್ತು ಮಾಲಿನ್ಯಕಾರಕಗಳನ್ನು ಪರಿಣಾಮಕಾರಿಯಾಗಿ ಚಿಕಿತ್ಸೆ ನೀಡಲಾಗುತ್ತದೆ ಎಂದು ಖಚಿತಪಡಿಸಿಕೊಳ್ಳಲು ವೆಲ್ಡಿಂಗ್ ಮೇಲ್ಮೈಯನ್ನು ಸಮರ್ಪಕವಾಗಿ ಸ್ವಚ್ಛಗೊಳಿಸಲು ಮತ್ತು ಪೂರ್ವ-ಚಿಕಿತ್ಸೆ ಮಾಡುವುದು ಪರಿಹಾರವಾಗಿದೆ.
4. ವೆಲ್ಡಿಂಗ್ ಹೀಟ್ ಇನ್ಪುಟ್ನ ಅಸಮರ್ಪಕ ನಿಯಂತ್ರಣ: ವೆಲ್ಡಿಂಗ್ ಸಮಯದಲ್ಲಿ ಶಾಖದ ಇನ್ಪುಟ್ನ ಕಳಪೆ ನಿಯಂತ್ರಣ, ಉದಾಹರಣೆಗೆ ವೆಲ್ಡಿಂಗ್ ಸಮಯದಲ್ಲಿ ಅತಿಯಾದ ತಾಪಮಾನ, ವೆಲ್ಡಿಂಗ್ ಪದರದ ಅಸಮರ್ಪಕ ಕೂಲಿಂಗ್ ದರ, ಇತ್ಯಾದಿ, ವೆಲ್ಡಿಂಗ್ ಪ್ರದೇಶದ ರಚನೆಯಲ್ಲಿ ಬದಲಾವಣೆಗಳಿಗೆ ಕಾರಣವಾಗುತ್ತದೆ, ಇದರಿಂದಾಗಿ ಬಿರುಕುಗಳು ಉಂಟಾಗುತ್ತವೆ. .ಮಿತಿಮೀರಿದ ಮತ್ತು ತ್ವರಿತ ತಂಪಾಗಿಸುವಿಕೆಯನ್ನು ತಪ್ಪಿಸಲು ವೆಲ್ಡಿಂಗ್ ಸಮಯದಲ್ಲಿ ತಾಪಮಾನ ಮತ್ತು ತಂಪಾಗಿಸುವ ದರವನ್ನು ನಿಯಂತ್ರಿಸುವುದು ಪರಿಹಾರವಾಗಿದೆ.
5. ಸಾಕಷ್ಟು ಒತ್ತಡ ಪರಿಹಾರ: ವೆಲ್ಡಿಂಗ್ ನಂತರ ಸಾಕಷ್ಟು ಒತ್ತಡ ಪರಿಹಾರ ಚಿಕಿತ್ಸೆಯು ಬೆಸುಗೆ ಹಾಕಿದ ಪ್ರದೇಶದಲ್ಲಿ ಸಾಕಷ್ಟು ಒತ್ತಡ ಪರಿಹಾರವನ್ನು ಉಂಟುಮಾಡುತ್ತದೆ, ಇದು ಸುಲಭವಾಗಿ ಬಿರುಕುಗಳಿಗೆ ಕಾರಣವಾಗುತ್ತದೆ.ಶಾಖ ಚಿಕಿತ್ಸೆ ಅಥವಾ ಕಂಪನ ಚಿಕಿತ್ಸೆ (ಮುಖ್ಯ ಕಾರಣ) ನಂತಹ ವೆಲ್ಡಿಂಗ್ ನಂತರ ಸೂಕ್ತವಾದ ಒತ್ತಡ ಪರಿಹಾರ ಚಿಕಿತ್ಸೆಯನ್ನು ನಿರ್ವಹಿಸುವುದು ಪರಿಹಾರವಾಗಿದೆ.
ಲಿಥಿಯಂ ಬ್ಯಾಟರಿಗಳ ಉತ್ಪಾದನಾ ಪ್ರಕ್ರಿಯೆಗೆ ಸಂಬಂಧಿಸಿದಂತೆ, ಯಾವ ಪ್ರಕ್ರಿಯೆಗಳು ಬಿರುಕುಗಳನ್ನು ಉಂಟುಮಾಡುವ ಸಾಧ್ಯತೆಯಿದೆ?
ಸಾಮಾನ್ಯವಾಗಿ, ಸೀಲಿಂಗ್ ವೆಲ್ಡಿಂಗ್ ಸಮಯದಲ್ಲಿ ಬಿರುಕುಗಳು ಸಂಭವಿಸುತ್ತವೆ, ಉದಾಹರಣೆಗೆ ಸಿಲಿಂಡರಾಕಾರದ ಉಕ್ಕಿನ ಚಿಪ್ಪುಗಳು ಅಥವಾ ಅಲ್ಯೂಮಿನಿಯಂ ಶೆಲ್ಗಳ ಸೀಲಿಂಗ್ ವೆಲ್ಡಿಂಗ್, ಚದರ ಅಲ್ಯೂಮಿನಿಯಂ ಶೆಲ್ಗಳ ಸೀಲಿಂಗ್ ವೆಲ್ಡಿಂಗ್, ಇತ್ಯಾದಿ. ಜೊತೆಗೆ, ಮಾಡ್ಯೂಲ್ ಪ್ಯಾಕೇಜಿಂಗ್ ಪ್ರಕ್ರಿಯೆಯಲ್ಲಿ, ಪ್ರಸ್ತುತ ಸಂಗ್ರಾಹಕನ ವೆಲ್ಡಿಂಗ್ ಸಹ ಪೀಡಿತವಾಗಿರುತ್ತದೆ. ಬಿರುಕುಗಳಿಗೆ.
ಸಹಜವಾಗಿ, ಈ ಬಿರುಕುಗಳನ್ನು ಕಡಿಮೆ ಮಾಡಲು ಅಥವಾ ತೊಡೆದುಹಾಕಲು ನಾವು ಫಿಲ್ಲರ್ ತಂತಿ, ಪೂರ್ವಭಾವಿಯಾಗಿ ಕಾಯಿಸುವಿಕೆ ಅಥವಾ ಇತರ ವಿಧಾನಗಳನ್ನು ಸಹ ಬಳಸಬಹುದು.
ಪೋಸ್ಟ್ ಸಮಯ: ಸೆಪ್ಟೆಂಬರ್-01-2023